Snack Recall: Specific Potato Chip Batch
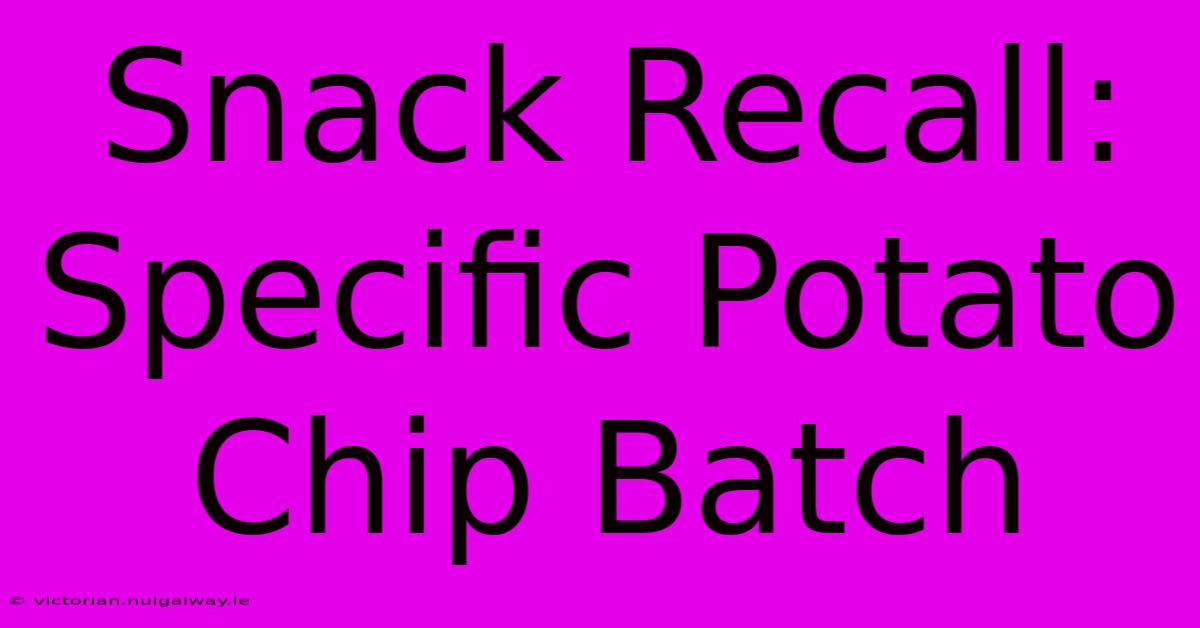
Discover more detailed and exciting information on our website. Click the link below to start your adventure: Visit Best Website. Don't miss out!
Table of Contents
Snack Recall: A Crunchy Crisis with a Specific Potato Chip Batch
So, you’re reaching for your favorite bag of [Brand Name] potato chips, ready for a crunchy, salty delight, when BAM! A recall notice slaps you in the face. This isn't just any recall; it's about a specific batch of chips. Let's delve into the salty depths of this crunchy crisis.
The Unexpected Crunch: A Recall Story Unfolds
Imagine this: it’s Friday night, the perfect time for a movie marathon and a bag of your go-to chips. You rip open the bag, only to discover…well, something's off. Maybe it's the smell, a slightly off-putting metallic tang, or perhaps the texture feels a little…gritty. Before you write it off as a bad batch (we've all been there), consider this: a recall for a specific batch of your beloved snack could be the reason behind your unusual experience.
Understanding the Gravity of Specific Batch Recalls
This isn’t some mass-market recall affecting every bag on the shelves. No, this is a targeted operation, indicating a precise problem within a single production run. Why is this significant? It suggests a highly localized issue – perhaps a malfunctioning machine, a contamination incident at a specific point in the production line, or even a rogue ingredient that slipped through the cracks. This level of specificity is crucial; it shows a proactive approach from the company, limiting the scope of the problem and hopefully preventing widespread issues.
Decoding the Batch Numbers: The Secret Code of Snacking
Have you ever stared at a tiny, almost invisible code on your snack packaging and wondered what it means? Well, in situations like these, it's the key to unlocking the mystery. Batch numbers are like tiny fingerprints, unique identifiers that pinpoint the exact moment and place of production. If your chips carry the designated recall batch number, it's crucial to take action.
What Happens When a Specific Batch is Recalled?
Recalls aren't just about protecting consumers; they're about preserving brand reputation. A swift and effective recall demonstrates accountability and shows the company cares about its customers' well-being. It's a significant undertaking, involving complex logistics, communication, and often, significant financial investment. The company usually outlines clear instructions on how to return the affected product, often offering refunds or replacements.
Why Specific Batch Recalls Happen More Frequently Now
In today’s fast-paced, highly automated food production world, recalls, while unfortunate, are almost inevitable. Sophisticated tracking systems allow for pinpointing problems with amazing precision. Think of it as a highly effective quality control mechanism, catching issues before they become widespread problems. While inconvenient, these targeted recalls ultimately protect consumers.
####### The Role of Technology in Preventing Future Incidents
Technology plays a crucial role in modern food production, from robotic arms assembling snack bags to sophisticated sensors monitoring production lines for anomalies. Artificial intelligence is also making its mark, improving quality control and predicting potential issues before they arise. These advances are helping to minimize the likelihood of future recalls and ensuring consumer safety.
######## The Human Element in Food Safety: Beyond Machines
While technology is crucial, the human element remains essential. Highly trained quality control professionals are the eyes and ears of the production process, constantly monitoring for deviations from the norm. Their keen observations and rigorous checks form a critical safety net, complementing the technology.
######### Consumer Responsibility: The Importance of Reporting Issues
If you notice something unusual about your snacks—an odd smell, unusual texture, or anything out of the ordinary—report it! Food safety is a collective responsibility. By reporting potential problems, you're contributing to a safer food supply for everyone.
########## The Aftermath of a Recall: Learning and Improvement
Recalls, while disruptive, offer valuable opportunities for learning and improvement. Companies rigorously investigate the cause, implement corrective actions, and enhance their quality control processes to prevent similar incidents in the future. This continuous improvement cycle is vital for building consumer trust and ensuring food safety.
########### The Impact on the Food Industry: A Ripple Effect
A recall, especially of a popular product like potato chips, can have a significant impact on the food industry. It affects not only the company involved but also its suppliers, distributors, and ultimately, consumer confidence. It’s a stark reminder of the importance of maintaining stringent quality control measures throughout the entire supply chain.
############ Beyond the Crunch: A Broader Look at Food Safety Regulations
Recalls are governed by stringent regulations, ensuring consumer safety and accountability. Government agencies play a vital role in monitoring food production, investigating incidents, and enforcing regulations. These regulations are constantly evolving to meet the challenges of a dynamic food industry.
############# The Future of Food Safety: A Constant Evolution
Food safety is a continuous journey, not a destination. As technology evolves, so too will food safety practices. We can expect even more sophisticated monitoring systems, data analytics, and AI-driven solutions to further enhance food safety in the years to come.
############## The Power of Transparency: Keeping Consumers Informed
Transparency is paramount in building consumer trust. Open communication regarding recalls, including clear explanations of the issue and steps being taken to address it, is essential. This transparency fosters a sense of confidence and reinforces the commitment to food safety.
############### The Ethical Dimensions of Food Recalls
Recalling a product, especially a beloved snack, is a significant decision, carrying ethical and financial implications. However, prioritizing consumer safety should always be paramount, demonstrating a commitment to ethical business practices.
################ Beyond the Chips: A Wider Perspective on Product Recalls
Recalls are not limited to food products; they occur across various industries, from automobiles to pharmaceuticals. The underlying principle remains the same: consumer safety and accountability.
################# The Long-Term Implications: Building Consumer Trust
Overcoming the impact of a recall requires more than just fixing the immediate problem. It involves rebuilding consumer trust, reinforcing the commitment to safety, and demonstrating long-term accountability.
Conclusion:
The seemingly simple act of enjoying a bag of potato chips is connected to a complex web of production, regulation, and consumer safety. A specific batch recall highlights the importance of proactive quality control, transparent communication, and the crucial role technology plays in preventing future incidents. While inconvenient, these events underscore the commitment to keeping our snacks safe. It's a reminder that even the most enjoyable things in life are under constant scrutiny, ensuring that the next crunch is both satisfying and safe.
FAQs:
-
What if I ate chips from the recalled batch and feel unwell? Contact your doctor immediately and report the incident to the company that issued the recall. Retain the packaging for reference.
-
Can I still eat other batches of the same chips? Unless specifically stated in the recall notice, other batches should be unaffected. However, always check the batch number against the recall information.
-
How does the company determine which batch to recall? Through meticulous tracking systems that monitor production, identify anomalies, and pinpoint the source of the problem.
-
What types of problems typically lead to specific batch recalls? These can range from contamination to equipment malfunctions, incorrect labeling, or the presence of foreign objects.
-
What is the role of government agencies in these recalls? Agencies like the FDA (in the US) monitor the recall process, investigate the cause, and ensure that the company takes appropriate corrective actions to prevent future incidents.
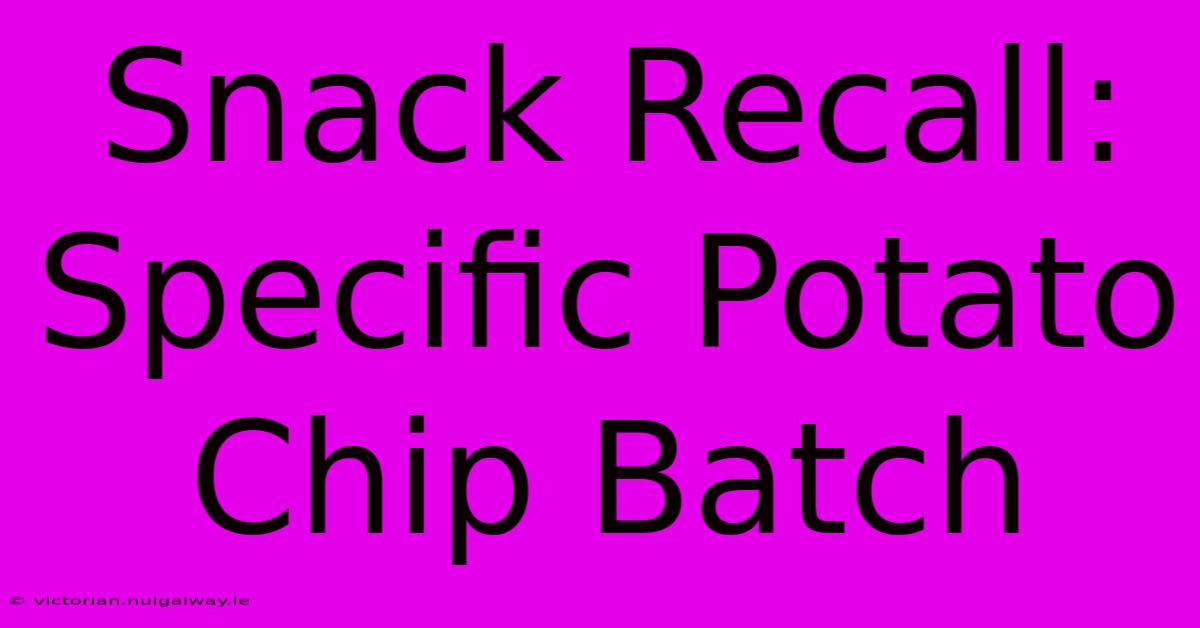
Thank you for visiting our website wich cover about Snack Recall: Specific Potato Chip Batch. We hope the information provided has been useful to you. Feel free to contact us if you have any questions or need further assistance. See you next time and dont miss to bookmark.
Also read the following articles
Article Title | Date |
---|---|
House Backs Hiltons Youth Reform Plan | Dec 19, 2024 |
Ex Nfl Star Vick Leads Norfolk Team | Dec 19, 2024 |
Vick Accepts Norfolk State Job | Dec 19, 2024 |
Nunez And Elliott Power Liverpool Past Southampton | Dec 19, 2024 |
Joint Venture Bbc Studios And Disney | Dec 19, 2024 |
Budget Impasse Trumps Rejection Of Funding Bill | Dec 19, 2024 |
Vicks Next Chapter Norfolk Coaching | Dec 19, 2024 |
Arsenals 3 2 Carabao Cup Win Live Updates | Dec 19, 2024 |
Bahamas Taps Herschel Walker | Dec 19, 2024 |
House Ethics Committee Releases Gaetz Report | Dec 19, 2024 |